The Benefits of 3D Laser Scanning—According to an IDI Client
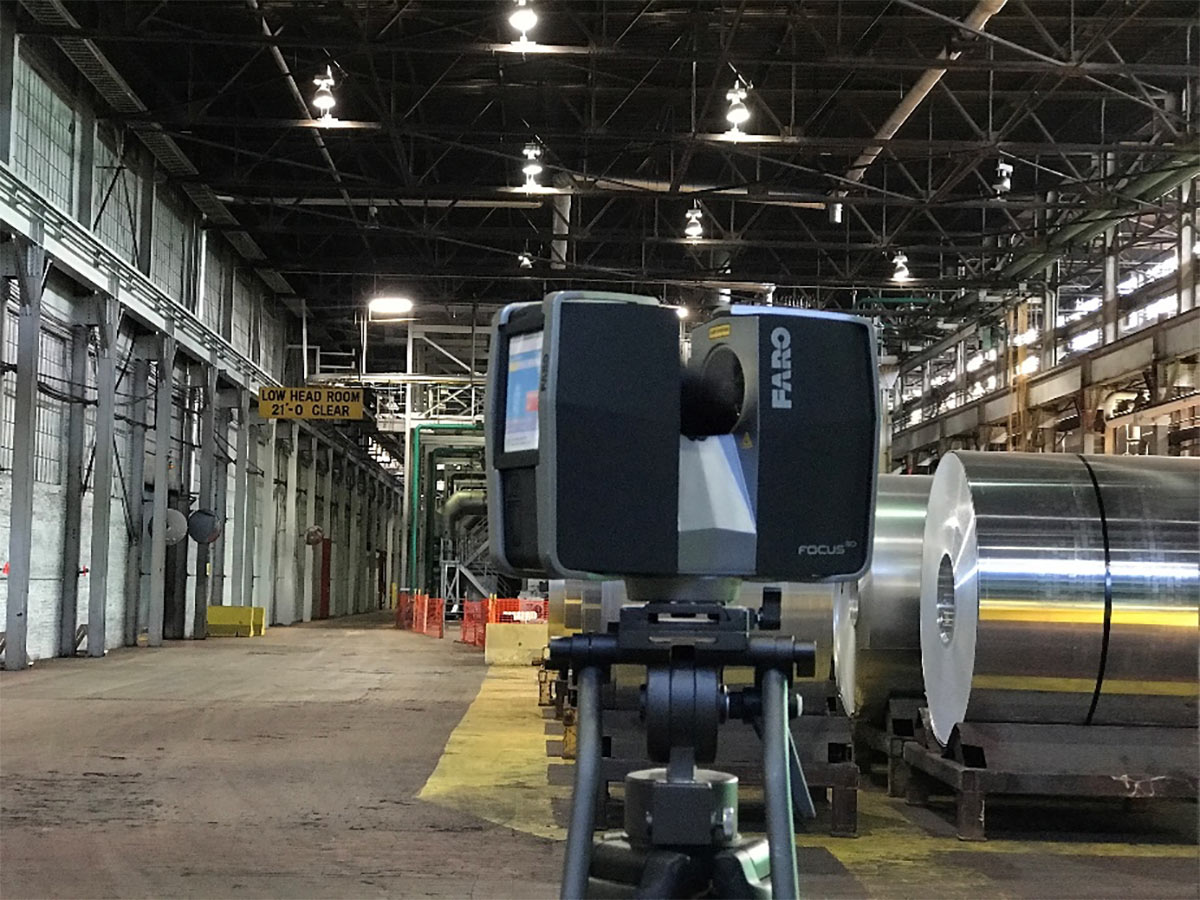
It’s one thing for us to tout the long list of benefits that our 3D laser scanning capabilities bring to the job. It’s another to hear it straight from the client. Bob Uncapher, the former resident engineer at 3M’s plant in Midway, Tennessee, reflected on a time when IDI and 3D scanning played a crucial role in a project there.
During an evaluation of the facility, the company’s risk team determined the supporting structures for two cranes did not meet the company’s minimum standards. Remediation wasn’t an option. “No one knew what kind of footers were underneath this monster,” says Uncapher. There was no documentation related to the decades-old system: no building or crane system drawings, documentation on footers, or as built utilities.
While the company had several 3D scanners at the time, the resources were largely based 1,000 miles away at the company’s headquarters. The expense and scheduling challenges posed by the distance and the requirement that much of the work be done on Friday evenings or over the weekend due to continuous production made IDI an appealing alternative.
The 15-ton crane systems were used to load and unload a number of furnace bodies and move the complete furnaces themselves, and Uncapher explains that achieving a tight fit within the existing building structure was key. “In some situations if something didn’t fit within 6 inches you might not care because it would still be functional. Here inches were critical; if runways were shortened the crane couldn’t service center of the furnace beneath it.”
The complexities of the whole system were such that to get a drawing of where all the parts were was impossible. Crane structure and footer designs were required, and “scanning proved invaluable because we knew where interference points were,” he says. “IDI has the expertise to take a point cloud and turn it into beams, pipes, and furnaces,” reflects Uncapher. “The point cloud itself can be a lot of noise. Interpreting that and turning it into a model that accurately reflects what’s in the field and is something you can use is another level of expertise that not everyone has.”
The cost and time savings piled up: No additional measurement trips were necessary and all modifications were made in the initial modeling phase, with no steel modifications required in the field. The footers were installed accurately and with no interference with existing building footers or underground utilities. The project was completed on schedule and on budget.